As one of the solids control equipments and drilling waste management system manufacturer in China, GN solids control also produce oil sludge treatment system with treating capacity 1 ~2 m3/h, 5m3/h, 15m3/h for option.
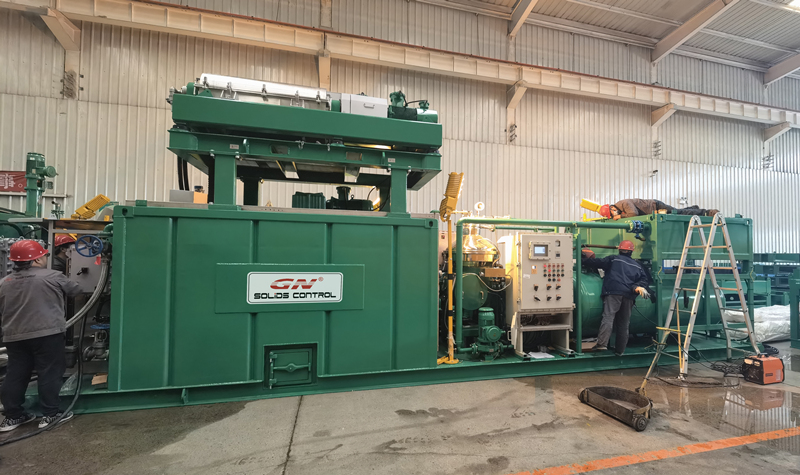
GNOST-05A oil sludge treatment system with 5m3/h treating capacity, the main equipments including double deck shale shaker, VFD decanter centrifuge, 3 phase separator, vacuum pump, if the budget is limited and required treatment result is not main concern, we can use 3 phase decanter centrifuge instead of VFD decanter centrifuge and 3 phase separator. The 3 phase disc separator is suitable for three phase liquid liquid solids separation, such as oil water and solids separation, but the pre-condition to feed into the 3 phase disc separator is that solids content should be lower than 3%.
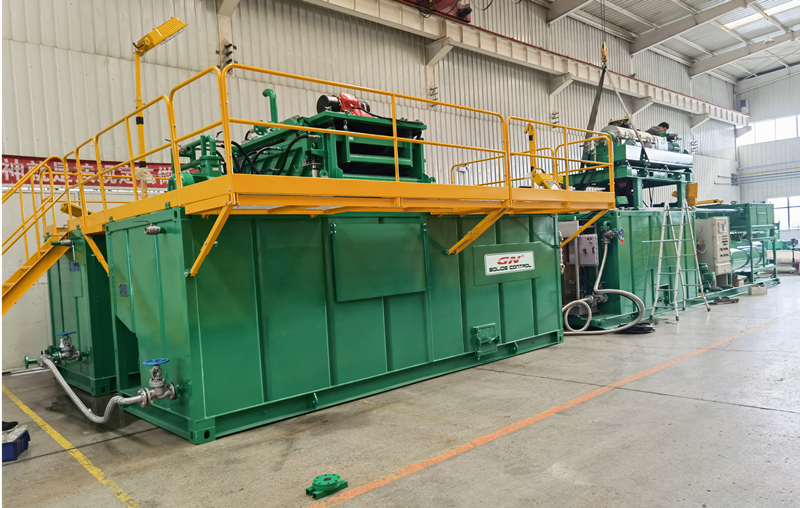
If the oil sludge with higher solids content and coarse solids size, the user should use drying shaker separation modular to separate big solids and reduce solids content, then feed to 2 phase separation decanter centrifuge to separate fine solids from liquid, so that most of the solids will be separated out, and the oil water mixture fluids can be feed to 3 phase disc separator. If the original oil sludge to be treated is with high viscosity and very low fluidity, to improve the oil separation efficiency of the solids, proper chemicals can be jetted into the oil sludge in the pre-mixing tank and mixed by mud agitator continuously, the prepared mixed oil sludge will be transferred by submersible slurry pump and feed to drying shaker to separate big size solids. The oil sludge is transferred by sludge vacuum pump from waste pit to pre-mixing tank. The containerized chemical dosing system can add proper chemicals into the fluids for easier separation of ultra fine solids by decanter centrifuge from oil sludge.